This is an extension of this previous thread of mine: https://www.technibble.com/forums/threads/best-30-solder-gun-for-dc-jack-repair.71966/#post-568362
I want to get into repairing DC jacks on laptops. It was recommended that I purchase a hot air reflow station. I watched some soldering videos and it appears that Kendal is a very popular brand. On Amazon I found a 2-in-1 Kendal station that has both a hot air reflow tool and solder iron. See here.
I have never soldered before, but the following seems like a great soldering process: (**please critique**)
Got this info from this video
.
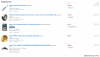
.
At what temperature and fan speed will I want to set the hot air flow gun and at which angle and distance will I want to use it?
.
.
Keep the tip clean while you work. Have a damp sponge handy to occasionally wipe your tip on while soldering to remove residues that collect. A properly cleaned tip is bright and shiny. Keeping the tip clean is important but constantly wiping it on a wet sponge can cause early tip failure. Excessive wiping causes the tip temperature to repeatedly rise and fall (cycle) and the different metal layers in the tip to repeatedly expand and contract. This leads to metal fatigue and ultimately tip failure where the copper core bubbles out. There are brass wool coils that are used like a sponge to wipe the tip off on as you solder and will not cool the tip.
.
.
.
------------------------------------------------------------------------------------------------------------------------------
Some information about solder you might find useful
I was glad to find real tin-lead solder is still available! But reading the user reviews made me realize that some users were having problems because they don't fully understand solder and soldering. So here are a few tips some of you might find helpful:
1. Solder is used as a kind of glue to hold pieces of metal together and conduct electricity and heat between them.
2. To do this, you need to apply a metal that has a melting point lower than any of the metals being joined, else they will melt first.
3. For almost all electrical work, we could use lead, which is very cheap, but melts at about 328C (622F). Tin is expensive, but melts much more easily, at 232C (450F).
4. If we mix tin and lead together, we get an alloy which melts even more easily. It turns out that 60% tin and 40% alloy (60/40), like this solder, melts at 188C (370F). Even better, but more expensive and hard to find, is 63% tin and 37% lead, which melts at about 183C (361F). Plumbers use 50% tin and 50% lead alloy, melting at about 214C (418ºF). Avoid it for electrical/electronic work.
5. To get a good solder joint, the parts to be joined MUST be clean! Use a wire brush or sandpaper (not steel wool, bits of which can drop on your work and create short circuits.
6. Wrap the CLEAN wires together or clamp your CLEAN work so it will not move after you remove the soldering iron. Press the hot iron against the joint and touch the solder wire to the iron tip where it contacts the joint. Let a very small amount of solder melt and get drawn into the joint to help heat to travel into the joint. Then touch the solder to the part being soldered. To get a good joint, the JOINT, NOT THE IRON must melt the solder. The solder MUST "wet" the joint and flow into the joint smoothly. Move the iron away carefully and let the solder cool. It takes a few seconds for the melted solder to cool. During this time, the alloy is slushy, and movement before it cools will result in a weak, rough-looking "cold solder joint" which is unreliable and must be re-melted. Do not try to melt a blob of solder onto the iron's tip and carry it to the joint. The flux will be gone and the solder won't flow properly.
7. The slushy phase is very short for 60/40 solder, but can last for many seconds for 50/50. Plumbers used to take advantage of this to make "wipe joints" by wiping and forming the slushy solder with a rag as it cools. That is very seldom done these days--and NEVER in electronics. 63/37 solder goes from a liquid to a solid almost instantly, making cold joints rare. Buy it if you can; you use very little per joint in electronic work. I bought a 1-lb spool of it many years ago and still have most of it. I misplaced it recently, which is why I am here on Amazon.
8. Flux: Most metals quickly react with air to form an oxide film, starting as soon as they are cleaned. Aluminum is a very active metal, which would be unusable outdoors if its oxide film were not protecting it from corrosion. It makes soldering it very difficult, so it's usually crimped or welded.. Copper and brass oxide films will also prevent solder from adhering, so even if you CLEAN before soldering, you need a flux to dissolve and prevent oxidation at the joint during soldering. Acid flux is used in plumbing as it is very effective, but it is corrosive and must be removed after the joint is made. Rosin-based flux is less corrosive and can be left in place. It is usually supplied within the center core of electronic solder such as this, so you don't need to buy a can of it unless you are plumbing.
The secret of soldering: Lots of heat, for a very short time. Trying to protect parts from heat by using a low-temperature or undersized iron will actually result in MORE overheating of the parts because the heat will have more time to travel to the part even if the solder joint is unsuccessful. Do this: Use a good temperature-controlled soldering iron such as aWeller W60P 60Watts/120V Controlled Output Soldering Iron with a 1/16" or 1/8" tip for electronics or up to a 1/4" tip for heavier work. I use 600F temperature tips for 60/40 solder, though 700F might be better for lead-free solder. Keep the tip clean by melting a bit of solder on it and wiping it off quickly with a damp paper towel or sponge to get a smooth silvery surface. Modern irons come with iron-plated tips for long life. NEVER try to file them like you grandfather did!
If you are a newbie, you ought to get a training kit to start. I have been buying Elenco AmeriKit Learn to Solder Kits for my kids, nieces, nephews, and friends who want to learn to solder. These come with decent tools (though the soldering iron is not going to last 40 years like my W-60.) There is an excellent instruction sheet for soldering and desoldering, with a simple circuit board and parts to work with and hopefully build a working gadget. All at a remarkably low price.
I want to get into repairing DC jacks on laptops. It was recommended that I purchase a hot air reflow station. I watched some soldering videos and it appears that Kendal is a very popular brand. On Amazon I found a 2-in-1 Kendal station that has both a hot air reflow tool and solder iron. See here.
- The hot air tool can also be used to remove MacBook and smartphone screens.
I have never soldered before, but the following seems like a great soldering process: (**please critique**)
- Apply heat resistant tape to the areas around the DC jack to prevent heat damage to other components.
- Put fresh solder onto the solder joint to help transmit heat using the soldering iron.
- Solder has flux in its core to make the metal clean, but additional flux paste should be brushed on the solder joint to make the solder joint even cleaner.
- What do you recommend for flux paste?
- Use the heat gun to melt all of the soldering joints.
- Once the solder is molten, use a solder sucker to extract the old solder until you create a hole in the board where the joint was and can see through it. Add additional heat as needed to keep the solder molten.
- What do you recommend for a solder sucker? This one seems to be highly regarded. Or a de-soldering iron.
- Gently wiggle the old DC jack using needle-nose pliers and apply heat if necessary.
- Clean the solder joints with rubbing alcohol and an anti-static bristle brush
- Put the new jack in place. It has metal pieces that slip into the solder joint holes.
- Add new solder beads using the soldering iron.
- Put the thermal tape back in place.
- Apply fresh flux paste.
- Use the heat gun to melt the solder beads so they fill in the holes they were placed over.
- Clean the solder joints again.
Got this info from this video
.
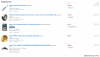
.
At what temperature and fan speed will I want to set the hot air flow gun and at which angle and distance will I want to use it?
.
.
Keep the tip clean while you work. Have a damp sponge handy to occasionally wipe your tip on while soldering to remove residues that collect. A properly cleaned tip is bright and shiny. Keeping the tip clean is important but constantly wiping it on a wet sponge can cause early tip failure. Excessive wiping causes the tip temperature to repeatedly rise and fall (cycle) and the different metal layers in the tip to repeatedly expand and contract. This leads to metal fatigue and ultimately tip failure where the copper core bubbles out. There are brass wool coils that are used like a sponge to wipe the tip off on as you solder and will not cool the tip.
.
.
.
------------------------------------------------------------------------------------------------------------------------------
Some information about solder you might find useful
I was glad to find real tin-lead solder is still available! But reading the user reviews made me realize that some users were having problems because they don't fully understand solder and soldering. So here are a few tips some of you might find helpful:
1. Solder is used as a kind of glue to hold pieces of metal together and conduct electricity and heat between them.
2. To do this, you need to apply a metal that has a melting point lower than any of the metals being joined, else they will melt first.
3. For almost all electrical work, we could use lead, which is very cheap, but melts at about 328C (622F). Tin is expensive, but melts much more easily, at 232C (450F).
4. If we mix tin and lead together, we get an alloy which melts even more easily. It turns out that 60% tin and 40% alloy (60/40), like this solder, melts at 188C (370F). Even better, but more expensive and hard to find, is 63% tin and 37% lead, which melts at about 183C (361F). Plumbers use 50% tin and 50% lead alloy, melting at about 214C (418ºF). Avoid it for electrical/electronic work.
5. To get a good solder joint, the parts to be joined MUST be clean! Use a wire brush or sandpaper (not steel wool, bits of which can drop on your work and create short circuits.
6. Wrap the CLEAN wires together or clamp your CLEAN work so it will not move after you remove the soldering iron. Press the hot iron against the joint and touch the solder wire to the iron tip where it contacts the joint. Let a very small amount of solder melt and get drawn into the joint to help heat to travel into the joint. Then touch the solder to the part being soldered. To get a good joint, the JOINT, NOT THE IRON must melt the solder. The solder MUST "wet" the joint and flow into the joint smoothly. Move the iron away carefully and let the solder cool. It takes a few seconds for the melted solder to cool. During this time, the alloy is slushy, and movement before it cools will result in a weak, rough-looking "cold solder joint" which is unreliable and must be re-melted. Do not try to melt a blob of solder onto the iron's tip and carry it to the joint. The flux will be gone and the solder won't flow properly.
7. The slushy phase is very short for 60/40 solder, but can last for many seconds for 50/50. Plumbers used to take advantage of this to make "wipe joints" by wiping and forming the slushy solder with a rag as it cools. That is very seldom done these days--and NEVER in electronics. 63/37 solder goes from a liquid to a solid almost instantly, making cold joints rare. Buy it if you can; you use very little per joint in electronic work. I bought a 1-lb spool of it many years ago and still have most of it. I misplaced it recently, which is why I am here on Amazon.
8. Flux: Most metals quickly react with air to form an oxide film, starting as soon as they are cleaned. Aluminum is a very active metal, which would be unusable outdoors if its oxide film were not protecting it from corrosion. It makes soldering it very difficult, so it's usually crimped or welded.. Copper and brass oxide films will also prevent solder from adhering, so even if you CLEAN before soldering, you need a flux to dissolve and prevent oxidation at the joint during soldering. Acid flux is used in plumbing as it is very effective, but it is corrosive and must be removed after the joint is made. Rosin-based flux is less corrosive and can be left in place. It is usually supplied within the center core of electronic solder such as this, so you don't need to buy a can of it unless you are plumbing.
The secret of soldering: Lots of heat, for a very short time. Trying to protect parts from heat by using a low-temperature or undersized iron will actually result in MORE overheating of the parts because the heat will have more time to travel to the part even if the solder joint is unsuccessful. Do this: Use a good temperature-controlled soldering iron such as aWeller W60P 60Watts/120V Controlled Output Soldering Iron with a 1/16" or 1/8" tip for electronics or up to a 1/4" tip for heavier work. I use 600F temperature tips for 60/40 solder, though 700F might be better for lead-free solder. Keep the tip clean by melting a bit of solder on it and wiping it off quickly with a damp paper towel or sponge to get a smooth silvery surface. Modern irons come with iron-plated tips for long life. NEVER try to file them like you grandfather did!
If you are a newbie, you ought to get a training kit to start. I have been buying Elenco AmeriKit Learn to Solder Kits for my kids, nieces, nephews, and friends who want to learn to solder. These come with decent tools (though the soldering iron is not going to last 40 years like my W-60.) There is an excellent instruction sheet for soldering and desoldering, with a simple circuit board and parts to work with and hopefully build a working gadget. All at a remarkably low price.
Last edited: